For manufactures, wholesale and industry
years of experience.
10,000 wheel variations.
We are happy to help you! Contact us without obligation if you have any questions or would like to request a quote. Our personal customer service pursues the goal of finding the best solution for each of our inquiries.
High capacity
Tested quality
High-tech machinery
Scalability
Professional employees
Handmade
Individual advice
Barcodes of the customer
Our way to quality wheels
For many, a wheel is just round and must rotate. From our experience as a manufacturer of millions of wheels of various types and requirements over the past decades, we know that quality begins with the selection of the appropriate individual components. The knowledge of our own strengths and possibilities creates a range of work that our partners appreciate.
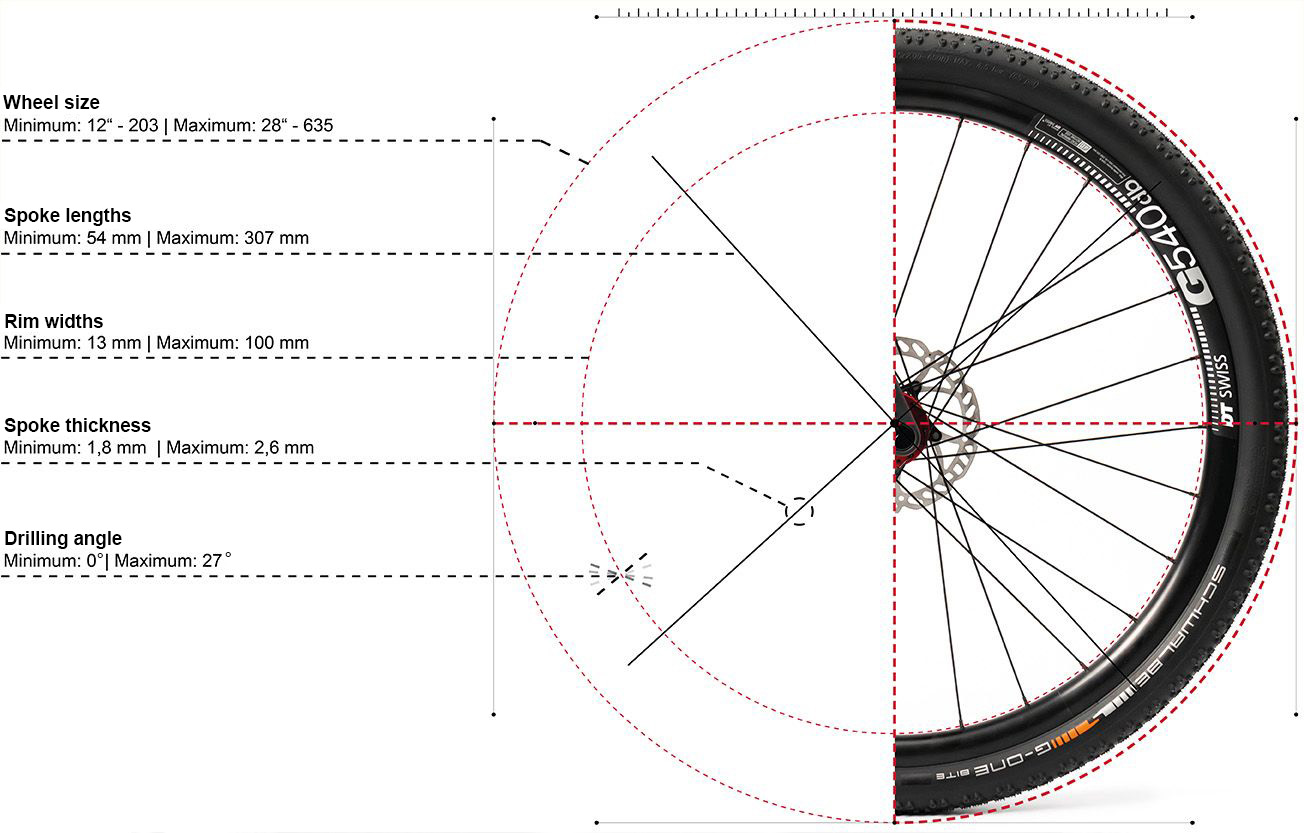
Component selection
A wheel to be manufactured consists of many different parts:
Rim tape |
Tires |
Tube |
Spoke |
Nipple |
Rim |
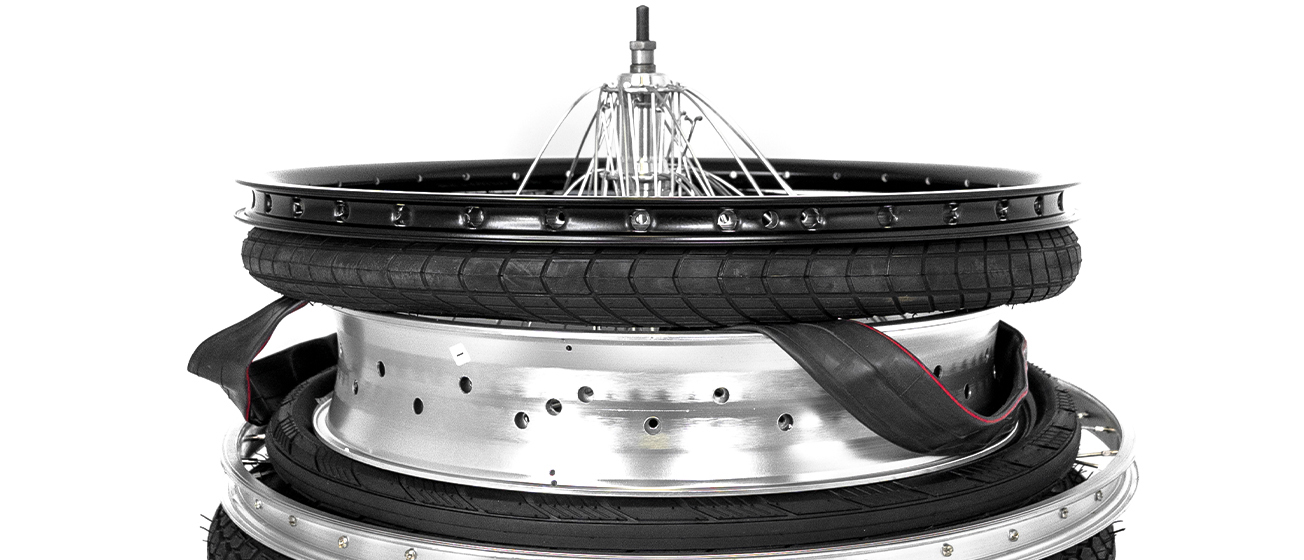
With regard to the qualitative demands of wheel construction, we look to a wide range of selected suppliers,
with which we have been working together in part for decades:
Choice of the necessary work steps
Based on the requirements for the use of the wheel, a technical and practical prototype is built in each case. As a result, an implementation plan is created from various work steps and the assigned machine options or determination of the manual work portion.
The following steps are available for selection:
- Alternating,
- One-sided inside,
- One-sided outside.
It is important for us to check the correct fit of spoke head in the assigned spoke hole of the hub as well as the matching spoke angle to the flange width.
- wheels packed individually in a cardboard box
- wheels packed in pairs in a carton
- wheels packed in carton (4 pcs.)
- wheels packed in carton (10 pcs.)
- wheels packed in EURO box pallet (exchange system)
- wheels packed in wheel rack (for pickup and return in direct transport)
Machine production is good - sometimes only manual labor helps
When is "good" really good? - or - the definition of (manufacturing) tolerances
A well-spoked and centered wheel is characterized by smooth running. Depending on the intended use of the respective wheel, the requirements are not the same in every case:
- A running wheel for strollers regularly reaches lower speeds,
- The use of wheels in cargo vehicles entails special requirements with regard to stability,
- Sporty wheels for use in triathlon bikes require high torsional and lateral stiffness despite low weight,
- …, the list could be extended infinitely.
Thus, details and associated tolerances are defined in coordination with customer expectations:
Spoke length |
Spoke crossings |
Spoke tension |
Late runout |
Altitude shock |
Centricity |
Offset |
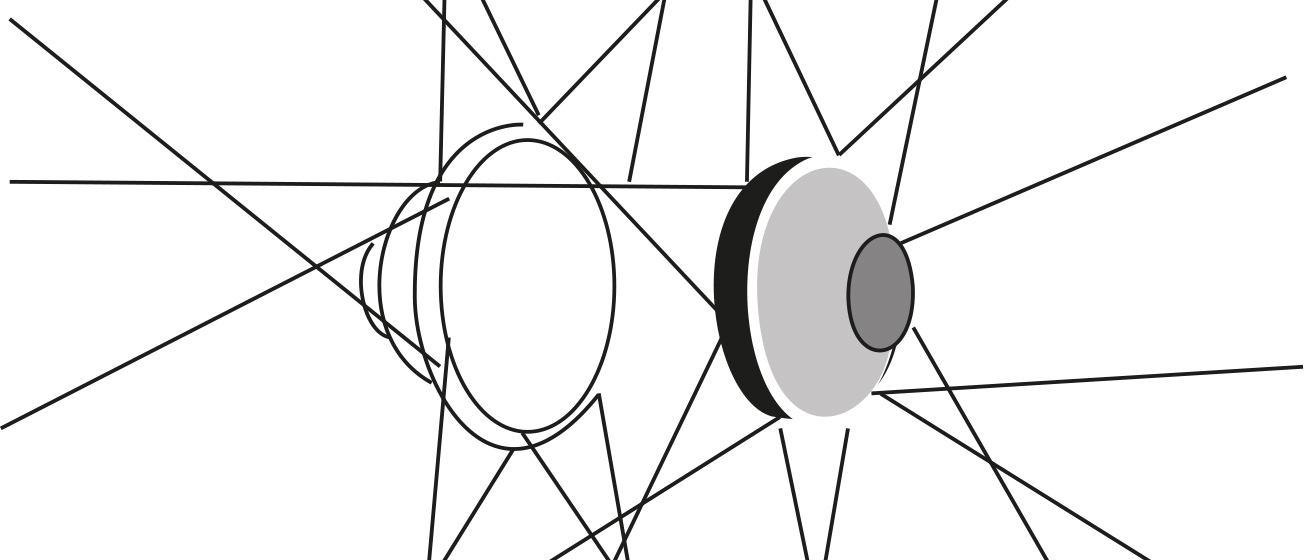
Tested quality
With the aim of meeting our standards and customer requirements, each project begins with an article summary in the document management system. By means of an article master file, the basic conditions for components and production are defined and then refined and checked in the prototyping process. Thus, the qualitative journey already starts at the goods receipt of new products by carrying out an initial inspection. While the individual parts are assembled into wheels in the respective work steps, the wheels are tested for target achievement at the end of production according to specified proportions:
- Are there any material damages or optical defects due to the machine production?
- Were all tolerances observed?
- Is the spoke pattern correct?
A digital test report underlies every production order and ensures the standard.
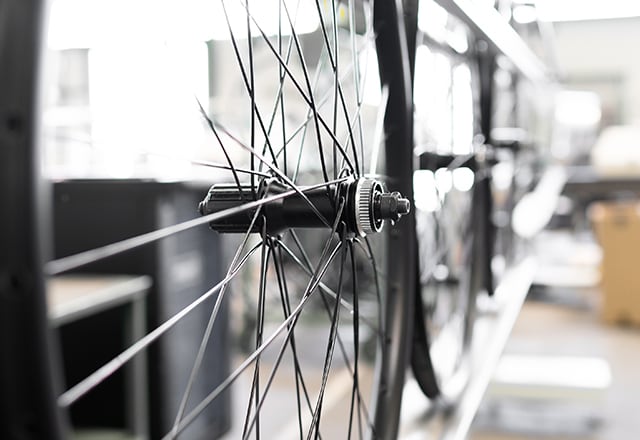
Packaging
True to the motto "...a product is only as good as it is received by the customer...", we fulfill various requirements of our customers and at the same time try to proceed in a resource-saving way. Possible is
- Wheels individually packed in cardboard box,
- Wheels packed in pairs in cardboard box,
- Wheelspacked in carton (4 pcs.),
- IWheels packed in carton (10 pcs.),
- Wheels packed in EURO box pallet (exchange system),
- Wheelsto be shipped packed in wheel rack (for pickup and return direct shipping).
In this process, all deliveries are protected separately by using reusable materials for padding.
Supporting the storage process of our partners, we offer customer-specific labels which enable the automatic scanning and booking of the goods. This can be done by means of a cardboard label or a spoke label directly on the wheel.
You are interessted in our wheel production?
Contact us:
Telephone +49 4474 9483-0
Fax +49 4474 9483-33
E-Mail contact@roland-werk.de